Clay refractory brick
Clay refractory brick is refractory clay refractory products. It is widely used in industry. Clay brick refractory bricks are divided into ordinary clay bricks, clinker clay bricks, clay bricks and high-silica content of clay bricks and other varieties.
Clay refractory brick is acidic refractory material, with the brick Al2O3 content increases its acid gradually weakened. Its thermal conductivity is the lowest of all refractory materials. Although the fire resistance of up to 1700 ° C, but the load softening temperature is only about 1300 ° C, which is the biggest drawback of clay bricks, it can not be used at high temperatures, can not be under pressure. When it is attacked by a large amount of R2O, its softening temperature is further reduced to about 1050 ° C, so it can only be used in the lower part of the wall or in the lower part of the bottom.
Clay refractory brick thermal expansion rate is the smallest of the commonly used refractory materials. At the same time due to the small crystalline clay brick, stomata small and evenly distributed, so that the stress is easier to be buffered, so in a wide range of thermal shock resistance. Low temperature in the lower part of the regenerator Plaid bricks, flue and day glass furnace Furnace refractories near the feeder such as punch, bowl and other places require good thermal shock resistance, can play its role.
Clay brick manufacturing methods are more, you can hand molding, ramming molding, extrusion molding, mud casting and molding machine and other high-pressure molding. Different molding methods, the nature of products are very different. Even the chemical composition of the same type of raw materials, but also because of its different methods of forming brick caused by different properties. According to different parts of the use of different molding methods. Regenerative cells Lattice brick, brick size is small, with high pressure press molding products for the best; for large pool wall tiles, trough tiles and other vacuum exhaust using the best mud casting method; and the size of the exact product Molding method better.
The clay bricks used by friends all know that clay bricks are very useful, but sometimes we will meet the damaged clay bricks, and this is damaged brick that is due to the firing time is too high temperature formed, so that We need to control the firing temperature, today we will introduce the burning of clay brick needs to control the size of it.
Clay refractory bricks at the time of firing the level can be divided into a and two, in the time of its firing temperature is about 1440 ℃, up and down ups and downs can not exceed 50, the usual holding time is 40h. However, when faced with three levels of clay brick temperature control 1400 ℃, insulation moment is shorter than the previous two. I met in the tunnel using a second grade refractory fired at a temperature of 1500-1560 at the mercy of the temperature scale. Depending on the firing of different materials and finished products, the rate of warming is not the same. The rising temperature should be controlled at 600 ℃, and then start to change a little bit according to the difference, until the temperature is 1200 ℃. There is that we should pay attention to the temperature of the cooling time to do a good job.
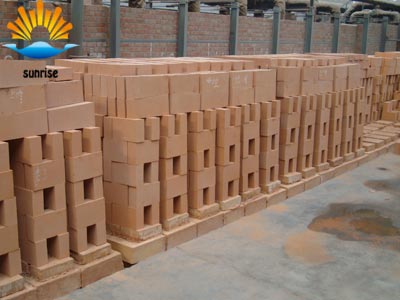