Factors that lead to erosion of glass furnace refractory bricks
Brick manufacturers analyze the factors that lead to the erosion of glass furnace refractory bricks: Glass melting furnaces are constructed from a variety of refractory materials. Different refractory materials used in different parts. Such as: direct contact with the liquid glass parts, the upper space and regenerative parts of the site. Production, due to erosion of these parts of different conditions, refractory erosion are also different. Firebrick erosion directly affects the life of the melting furnace, affecting the glass production, quality and energy consumption. Melting workers to understand the erosion of refractory bricks, no doubt on the production of great significance.
First, the melting furnace refractory bricks under erosion conditions
Furnace refractory bricks under erosion conditions, in general, should be from the temperature conditions, chemical erosion conditions, physical erosion conditions and time conditions to consider. These four conditions in the erosion of refractory bricks can not exist alone, must be a combination of several conditions. Such as brick heating or cooling process, which is the temperature and time of the two conditions, including both the rate of heating or cooling, but also the maximum temperature and the holding time, chemical etching conditions to remove the type and number of etchants, the temperature level, sustained The length of time and the number of times have a great impact; physical erosion conditions as well. Often physical erosion and chemical erosion often coexist. So in the glass melting furnace, the result of these four conditions together determine the rate of firebrick erosion.
The conditions under which the refractory bricks are eroded are the same for different parts of a furnace. The other three conditions are very different, each with its own special law.
A) temperature conditions
Most parts of the furnace are made of silica brick, and the change of the volume of the silica brick caused by the change of the crystal shape of the quartz during the baking process should be considered. Slow rise in general use of silica bricks do not burst the principle. In the cold repair of those who want to keep those silica brick masonry, but also to cool slowly to prevent damage. These are the most typical temperature conditions on the impact of refractory bricks.
Cold repair, the furnace into the continuous operation of the production period, the temperature system has strict rules and controls, the melting temperature of the furnace parts are allowed to fluctuate within the scope. Although the regenerator due to smell change to the reasons. Will result in a temperature change of about 300 ° C, but this will have little effect on most refractory bricks, except for special refractories, so from the point of view of the entire kiln, it can be said that temperature changes during normal operation do not damage the bricks Big.
So, in normal production, the maximum temperature of the furnace on the impact of refractory bricks? The maximum temperature zone of the furnace is a hot spot. Here refractory brick temperature up to 1650 ℃, even if the use of load softening temperature higher than 1650 ℃ high-quality silica brick, in actual production may also be strongly eroded, mainly because in addition to temperature conditions, there are other erosion conditions at the same time The result of the action.
Therefore, the glass furnace, the temperature conditions do not exist alone. Regardless of other erosion conditions, it is pointless to think solely of the effects of temperature. When there are other erosion conditions, temperature is a very important factor. When firebricks are subject to physical and chemical attack, the erosion rate is a function of temperature. The erosion rate increases with logarithm of temperature. Generally believed that the temperature increased by 50 ℃, refractory material erosion rate is doubled.
B) chemical erosion conditions
1, melting furnace refractory bricks suffered chemical erosion summed up the following four:
2, molten glass and refractory brick reaction caused by erosion;
3, glass compound dust and refractory chemical reaction caused by erosion;
4, glass and the reaction of volatile materials and refractories caused by erosion;
5, the fuel ash and combustion products and refractories caused by erosion.
In production, due to different parts of the furnace where the environment, the chemical corrosion reaction of the four kinds of occurrence and erosion are also different. For example, the first kind of erosion is represented by a pool wall brick which is in direct contact with the glass liquid. In addition to being chemically attacked by the glass liquid, the wall brick is also subject to the physical erosion of the erosion of the glass flow. The molten pool above the spatial structure and regenerative room there is no flow of physical erosion erosion, but by the other three kinds of erosion. Therefore, the study of refractory bricks erosion situation, it must be analyzed where it is located in the melting furnace may have the erosion conditions. Chemical resistance to firebrick subject to specific analysis of the specific circumstances.
C) physical erosion conditions
Physical erosion and time, temperature has a lot to do with. The most important physical erosion is the scouring effect of the glass flow and the gravity effect of the refractory load.
In the high temperature zone, the erosion of the molten glass solution will double the rate of chemical erosion. In the low temperature zone, the chemical erosion is very small, mainly due to physical erosion of the liquid erosion. When the melting furnace molten pool using electric melting and bubbling technology, the flow is more intense, intense erosion and chemical erosion with the firebrick will cause great damage.
Gravity damage caused by the load, mainly occurs in the regenerator lattice brick. Plaid body weight for the bottom of the lattice brick and bar 碹 pressure, when the chemical erosion will damage, in the damaged all due to stress concentration, often resulting in the collapse of the entire lattice body. In the ascending reheat furnace, the bearing capacity of the connection between the ascending path and the regenerator is not large, but the temperature is high and the amount of chemical attack is large, and the erosion is intense and easily destroyed under the load.
Furnace refractory bricks in addition to the erosion of the rhyme conditions in addition to the above, and the furnace structure design, operating conditions and building technology are related. Such as: kiln depth, cooling conditions, insulation measures, brick shape and arrangement, the flame is floating and the various parts of the heat load size, etc.} operating conditions in the feeding method, raw material conditions, hot spots, melting amount, fuel type, furnace Atmosphere, etc .; furnace technology brick refractory brick size, size error and the use of mud and so on. These issues all change temperature conditions, chemical attack conditions, and physical erosion conditions, thereby accelerating or slowing the erosion of refractory bricks. Finally, will reflect the time conditions that the melting furnace life. Melteners should take these factors into consideration, properly operate and maintain the melting furnace, minimize the erosion of refractory bricks, extend the furnace age, and improve the glass production and quality.
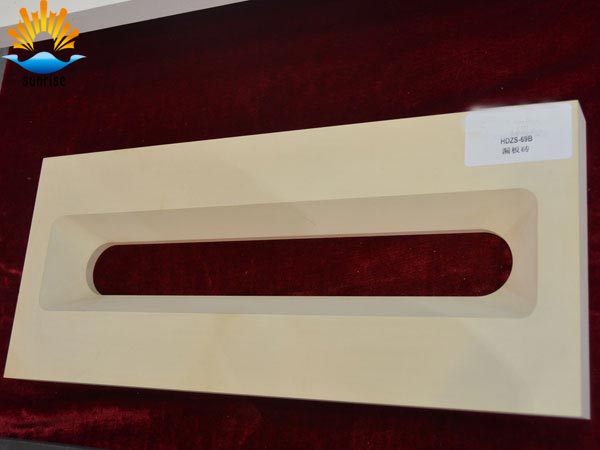