The characteristics of mullite insulation bricks
1. Foaming Foams for Lightweight Heat Preserved Bricks Bubbles with uniform bubble diameters can be obtained.
2. The foam is independent, and it is not easy to form connecting holes. The closed-cell rate of the foamed concrete prepared is high, and thus it has a good thermal insulation and waterproof effect.
3. Lightweight insulating bricks are used for the preparation of foamed concrete with a dry density of 300 to 1200 kg/m3, with less foam and good technical and economic benefits.
4, lightweight insulation brick and cement adaptability.
5, green, non-toxic, non-corrosive, safe to use.
6. The low price of lightweight insulation bricks can greatly reduce costs.
7, excellent foaming performance, foaming times up to 30 times.
The mullite insulation brick uses a wide range of high-quality refractory materials in the emerging industry. It has uniform expansion, excellent thermal shock resistance, high load softening point, high temperature creep value, high hardness, chemical resistance. Good characteristics, mullite insulation brick classification: mullite insulation brick according to the different density is mainly divided into light and heavy mullite brick, according to the use of different temperature is divided into: 1350 mullite brick, 1450 Mullite bricks, 1550 mullite bricks, etc.
The performance and application of mullite insulation bricks: high refractoriness, up to 1790°C. Load softening starting temperature 1600 ~ 1700 °C. Room temperature compressive strength 70 ~ 260MPa. Good thermal shock resistance. There are two kinds of sintered mullite bricks and fused mullite bricks. Sintered mullite bricks are made of high bauxite clinker, which is made by adding a small amount of clay or slaked clay as a binder and forming and firing. The fused mullite bricks are made of high alumina, industrial alumina and fire-resistant clay. Charcoal or coke fines are added as a reducing agent. After molding, they are manufactured by a reduction fused method. The fused mullite crystals are larger than sintered mullite and have better thermal shock resistance than sintered products. Their high temperature performance mainly depends on the alumina content and the uniformity of the mullite phase and glass distribution. Mainly used for hot blast stove top, blast furnace shaft and furnace bottom, glass melting furnace regenerator, ceramic sintering kiln, oil cracking system dead-end lining and so on.
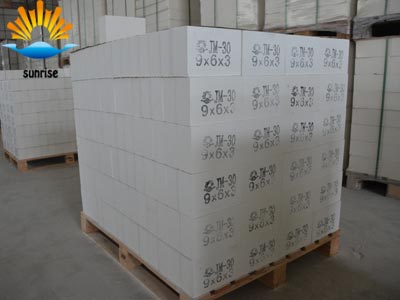