Different Positions And Structures Of Glass Furnace
The different parts of the glass furnace need using different refractory bricks, as the temperature, the erosion, the pressure and other things are different, below are the details for your reference.
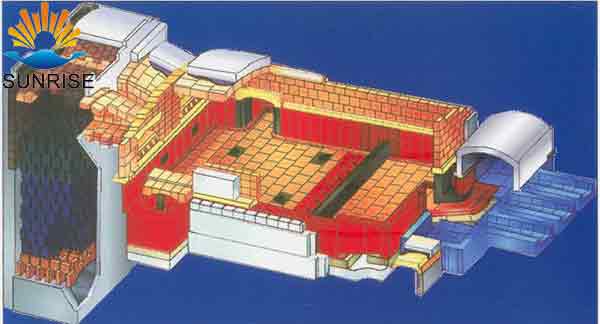
1. Sidewall brick
The ideal sidewall brick material of tank furnace containing molten sodium and calcium silicon material is fused cast AZS block. When melting alkali free or low alkali glass fiber, due to acid erosion, the sidewall brick should select fused cast AZS block or dense zircon brick.
2. Tank bottom brick
Tank bottom bricks are required to have wear resistance and integrity. The bottom generally adopts multi layer compound bottom structure, and the multilayer structure is generally in the insulation layer under the main layer of big fireclay bottom block. A protective layer and wear-resisting layer is above the big fireclay bottom block, and the protective layer adopts zirconium quartz sand or AZS Ramming Materials. Wear-resisting layer is over the protective layer and protects the tank bottom, and it contacts the glass liquid directly, so fused cast AZS block which has good corrosion and wear resistance is used in wear-resisting layer.
3. Doghouse brick
Doghouse is eroded by material powder and glass liquid, weared by material layer, crushed by flow liquid and influenced by flame, so damage is more serious. Therefore, refractory with high temperature resistance and corrosion resistance is needed, such as fused cast AZS block with 41%ZrO2 without shrinkage hole. Except for the corner bricks, other parts can adopt fused cast AZS block 33# with normal casting.
4. Throat brick
The liquid flow velocity in throat of glass furnace is the biggest and convects obviously which speed the corrosion. Throat brick usually adopts fused cast AZS block 41# without shrinkage hole
5. Cooling pool and solidification pool
When the glass liquid in cooling and solidification pool it has already melted and clarified, and getting into the late stage of the process. At this point, there absolutely can not cause any defect to the glass liquid. Fused cast AZS block is used in cooling pool duo to its high exudation temperature of glass liquid and it will not bring bubbles to the glass. Solidification pool always adopts fused cast α-β block.
6. Top crown and breast wall
The damage characteristics of this part is burning and erosion which has the requirement of stability to alkali vapor under high temperature and high refractoriness under load. So high quality silica brick or fused cast AZS block 33# can be adopted in this part.
7. Front wall and checker wall
Front wall and checker wall is two wall of melting part, and both of them has the characteristics of erosion and burning erosion, in addition, front wall which is one of the weak parts of furnace is influenced by wear erosion of material. Currently fused cast AZS block 33# is used, or high quality silica brick and sintered AZS block are compound used.
8.Special parts
There are some parts in glass furnace which has special application, such as bubbling brick, dam wall, electrode brick, peep hole and measure hole. The large temperature difference between inside and outside surface of bubbling brick can produce large mechanical stress, which can easily lead to cracking; Dam wall is easily damaged by the severe heat flow. So both these two parts can adopt fused cast AZS block with 41% ZrO2 without shrinkage hole. Electrode brick is strongly eroded by the circulating fluid flow around the electrode, and big temperature difference is caused due to the electrode cooling which produces large mechanical stress and leads to cracks of refractory bricks, so fused cast AZS block 41# without shrinkage hole is generally used as electrode brick. Peep hole and measure hole are easy to be burned by kiln overflowing flame, so fused cast AZS block 41# is used in these two parts.